Are you worried about your employees’ safety in the office? Electric shocks can occur unexpectedly and potentially harm your employees.
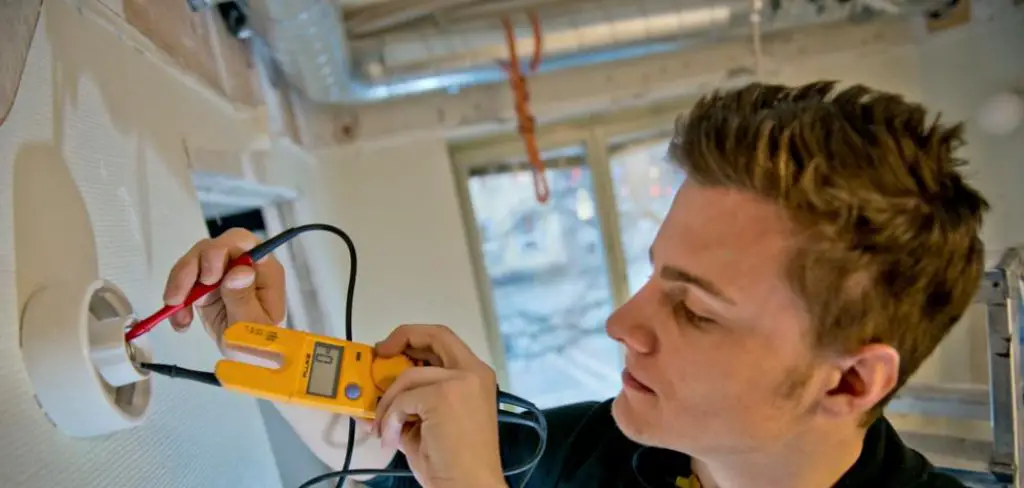
As a responsible employer, taking precautions and preventing electric shock hazards in the workplace is crucial. Electric shock can pose a significant risk in any workplace, mainly when electrical equipment is prevalent
Understanding the potential hazards and implementing effective prevention strategies is essential for ensuring the safety of employees.
This document outlines key practices and guidelines to help mitigate the risk of electric shock in the office, promoting a safer working environment for all.
By fostering awareness and establishing clear protocols, organizations can protect their workforce and maintain a culture of safety. Let’s dive into some of the key strategies on how to prevent electric shock in the office.
What Will You Need?
To effectively prevent electric shock hazards in the office, you must have some essential tools and resources. These include:
- A thorough understanding of electrical safety regulations
- Appropriate personal protective equipment (PPE)
- Regular maintenance and inspection of electrical equipment
- Proper training for employees on electrical safety procedures
- Clear communication channels for reporting any potential hazards or concerns
Once you have these in place, you can start implementing preventive measures to reduce the risk of electric shock in the office.
10 Easy Steps on How to Prevent Electric Shock in the Office
Step 1. Conduct Regular Risk Assessments
Begin by conducting thorough risk assessments to identify potential electrical hazards in your office environment.
This includes examining wiring, outlets, and equipment for any signs of wear and tear or improper use. Regular assessments help identify risks early, enabling timely interventions to prevent electric shock incidents.
Ensure that these assessments are documented and reviewed periodically, updating them whenever changes occur in the workplace.
Step 2. Ensure Proper Use of Electrical Equipment
It’s essential to educate employees on the correct operation and handling of electrical equipment.
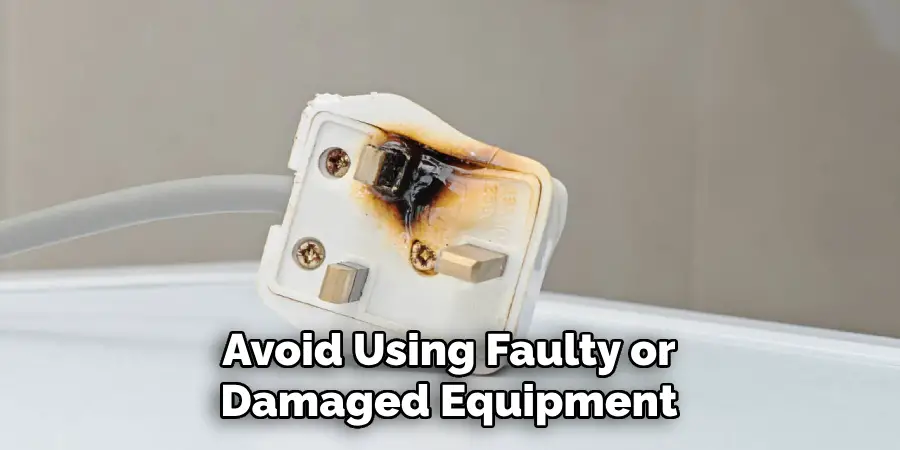
This includes following the manufacturer’s instructions, using tools and devices only for their intended purposes, and avoiding any makeshift connections.
Employees should also be trained to recognize and avoid using faulty or damaged equipment. The likelihood of electric shock can be significantly reduced by cultivating a culture of responsible equipment usage.
Regular reminders and training sessions can help reinforce these safety protocols within the workplace.
Step 3. Keep Workspaces Dry
Moisture is a significant contributor to electric shock risks. It’s vital to maintain dry conditions in all office areas, especially near electrical outlets and equipment.
Encourage employees to clean up any spills promptly and report leaks or water-related issues immediately. Installing mats or absorbent materials around moisture-prone areas can also help mitigate this risk.
Regularly check humidity levels and ventilation systems to ensure a dry environment, as dry conditions significantly decrease the likelihood of electric shocks.
Step 4. Use Ground Fault Circuit Interrupters (GFCIs)
Installing Ground Fault Circuit Interrupters (GFCIs) in areas where electrical equipment is used near water sources—such as kitchens, bathrooms, or break rooms—is a crucial safety measure.
GFCIs are designed to shut off the electrical circuit when they detect an imbalance in the current flow, which can indicate a leak of electricity that could lead to electric shock.
Regularly testing these devices to ensure their functionality will enhance safety in the workplace. Ensure all employees know the locations of GFCIs and understand how to reset them if they trip, ensuring quick response to potential electrical hazards.
Step 5. Regularly Inspect and Maintain Electrical Equipment
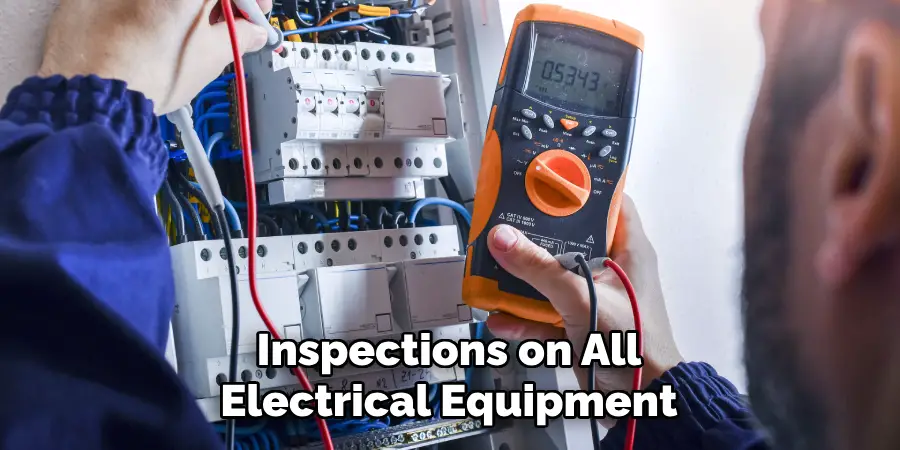
To prevent electric shocks, it’s essential to conduct routine inspections and maintenance on all electrical equipment used in the office. This includes checking for damaged cords, frayed wires, or any signs of wear that could increase the risk of electrocution.
Implement a scheduled maintenance plan that outlines the frequency of inspections and ensures that qualified personnel carry out repairs and replacements.
Keeping a log of inspections and maintenance activities will help track the condition of equipment and identify any recurring issues that need addressing.
Staying proactive with equipment upkeep can significantly reduce the likelihood of electrical incidents.
Step 6. Provide Personal Protective Equipment (PPE)
Appropriate personal protective equipment (PPE) is essential in safeguarding employees from electric shock hazards.
To minimize the risk of electrical injuries, equip workers with items such as insulated gloves, safety goggles, and rubber-soled footwear. Ensure all PPE complies with established safety standards and is regularly inspected for wear and tear.
-Additionally, training employees on the proper use and maintenance of PPE will empower them to take an active role in their safety, promoting a culture of diligence and preparedness in the workplace.
Step 7. Implement Lockout/Tagout Procedures
Lockout/tagout (LOTO) procedures are crucial in preventing electric shock during maintenance or repair work on electrical equipment. This safety practice involves isolating and de-energizing equipment before work begins, ensuring that employees are not exposed to live circuits.
Train employees on LOTO procedures, ensuring they understand the importance of securing energy sources and using appropriate tags to indicate that machinery is being serviced.
By implementing stringent LOTO practices, organizations can significantly reduce the risk of accidental energization, enhancing workplace safety. Regular audits and refresher training can help maintain compliance and awareness regarding these procedures.
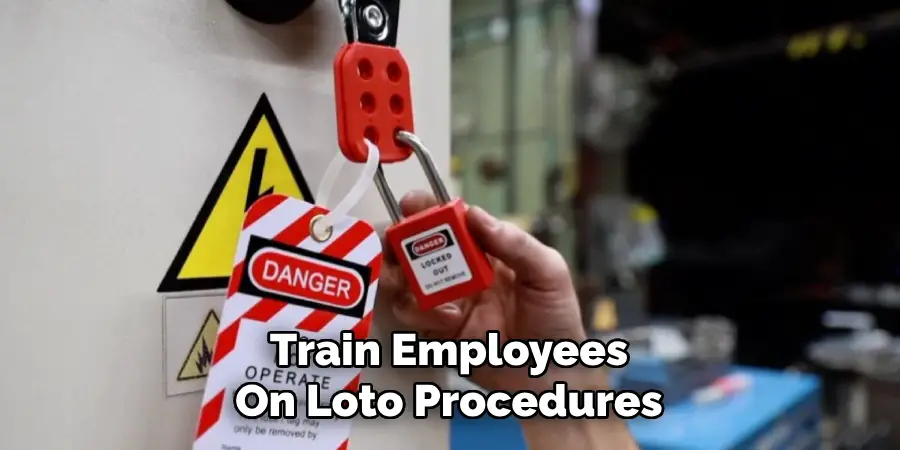
Step 8. Educate Employees on Emergency Procedures
Establishing clear emergency procedures related to electrical incidents, including electric shock, is imperative.
Training sessions should inform employees about how to respond during an electric shock, including emergency contacts, rescue techniques, and first-aid measures.
Employees should know the location of emergency equipment, such as fire extinguishers and first-aid kits, and how to access medical assistance quickly.
Regular drills can ensure that everyone is familiar with the emergency protocols, thus improving response time when an incident occurs. This proactive approach enhances employee safety and fosters a sense of preparedness in the workplace.
Step 9. Conduct Regular Safety Training
Ongoing safety training is essential for maintaining a safe working environment, particularly concerning electric shock prevention.
Schedule regular training sessions covering topics such as recognizing electrical hazards, safe work practices, and correctly using PPE and emergency procedures.
Engaging employees through hands-on demonstrations and interactive discussions can enhance retention of information and encourage a proactive attitude toward safety.
Providing periodic refresher courses ensures that all staff members remain informed about the latest safety protocols and any changes to regulations. By fostering a continuous learning culture, organizations can empower employees to actively participate in creating a safer workplace.
Step 10. Foster a Safety Culture
Creating a robust safety culture within the organization is vital for ensuring long-term commitment to electrical safety. Encourage open communication about safety concerns and establish channels for employees to report hazards without fear of reprisal.
Recognize and reward safe practices among staff, reinforcing the importance of safety in everyday operations. Regularly incorporate safety discussions into team meetings and promote the idea that safety is a shared responsibility.
By fostering a workplace environment prioritizing safety, employees are more likely to engage in proactive measures to prevent electric shock and other hazards, ultimately contributing to a safer and more productive workplace.
By following these steps, organizations can significantly reduce the risk of electric shock in the workplace and promote a culture of safety that prioritizes employee well-being.
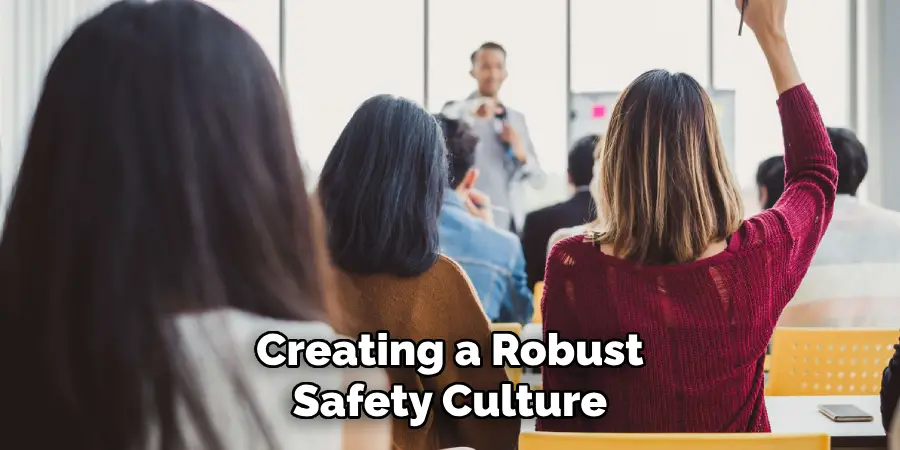
5 Things You Should Avoid
- Neglecting Regular Inspections: Avoid skipping routine inspections of electrical equipment and wiring. Failing to identify potential hazards like damaged cords and overloaded circuits can lead to severe accidents.
- Ignoring Training Needs: Don’t underestimate the importance of ongoing training. Avoid the mindset that employees don’t need further education on electrical safety and emergency procedures once employees are trained. Regular refreshers are essential.
- Using Damaged Equipment: Refrain from allowing the use of frayed or damaged electrical equipment. Always replace or repair faulty tools and devices immediately to prevent electrical hazards.
- Assuming Everyone Knows Safety Protocols: Never presume that all employees are aware of safety protocols and emergency procedures. Ensure that everyone is thoroughly trained and understands their role in maintaining a safe environment.
- Disregarding PPE Requirements: Avoid the mistake of not providing or enforcing the use of personal protective equipment (PPE). Employees should always have access to appropriate PPE, and its use should be strictly mandatory during any electrical work.
By avoiding these common pitfalls and implementing a comprehensive electrical safety program, organizations can significantly reduce the risk of electric shock incidents in the workplace.
Conclusion
In conclusion, how to prevent electric shock in the office demands a multifaceted approach that encompasses employee education, rigorous safety protocols, and a commitment to fostering a culture of safety.
By implementing comprehensive training programs, regular inspections, and proper use of personal protective equipment, organizations can effectively mitigate risks associated with electrical hazards.
Moreover, encouraging open communication about safety concerns and recognizing safe practices will further enhance the overall safety environment.
As a collective responsibility, every employee must be empowered to advocate for safety and adhere to established procedures, ultimately leading to a safer workplace for all.
Through diligent efforts, companies can not only protect their employees but also cultivate a proactive safety culture that prioritizes well-being and efficiency.